Custom Dip coating
Dip coating is the preferred solution when your entire product requires plastic coating (such as a wire rack), or has an odd shape or size where a standard cap or grip won’t work. Harman’s custom dip coating offers a competitive advantage for your unique product.
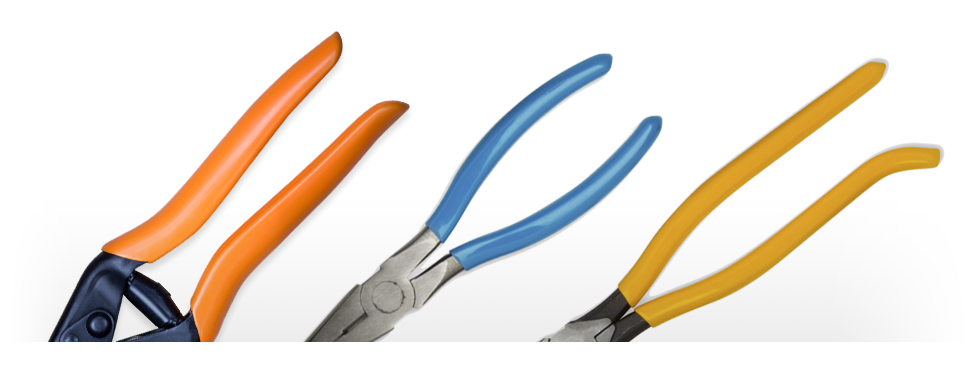
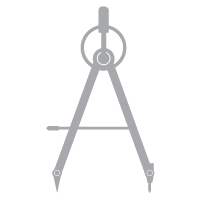
Expert Engineering
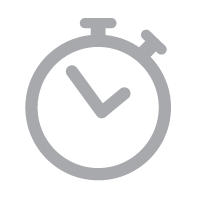
Rapid Prototyping
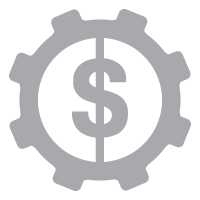
Affordable Tooling
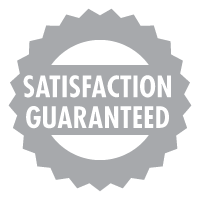
Quality Production
Materials
The superior finish comes from immersing your product in the highest quality Plastisol available. Because no fillers are used, the finish is free of surface blemishes for an exceptional look and feel.
finish
Whether high gloss or textured, dip coating provides a completely seamless surface that enhances and elevates the look of your finished product with a durable, safe and beautiful finish.
advantages
Dip Coating provides a protective shield that can be permanently bonded to your product if desired. The vinyl coating insulates against heat, cold, and electrical currents, and helps resist corrosion while providing a beautiful finished look and feel.
fast
Lead times are 7-10 business days after receiving a sample of the product to be dip coated, or a CAD drawing. Production ships within 4-6 weeks of sample approval. We engineer, prototype, build and ship from US based facilities which makes you productive more quickly.
uses
Dip Coating is often the process of choice for finished goods with odd shapes, wire racks, hand tools, toys and medical instruments because there is an almost limitless combination of colors, thickness and hardness (durometers) available.
service
We have created thousands of custom parts for clients like you. Because we do it every day, everyone on our staff is knowledgeable and the process is easy. You’ll have experts walking with you from concept, to prototype, through production.
Does your next project require a custom design?
Call our knowledgeable sales staff.